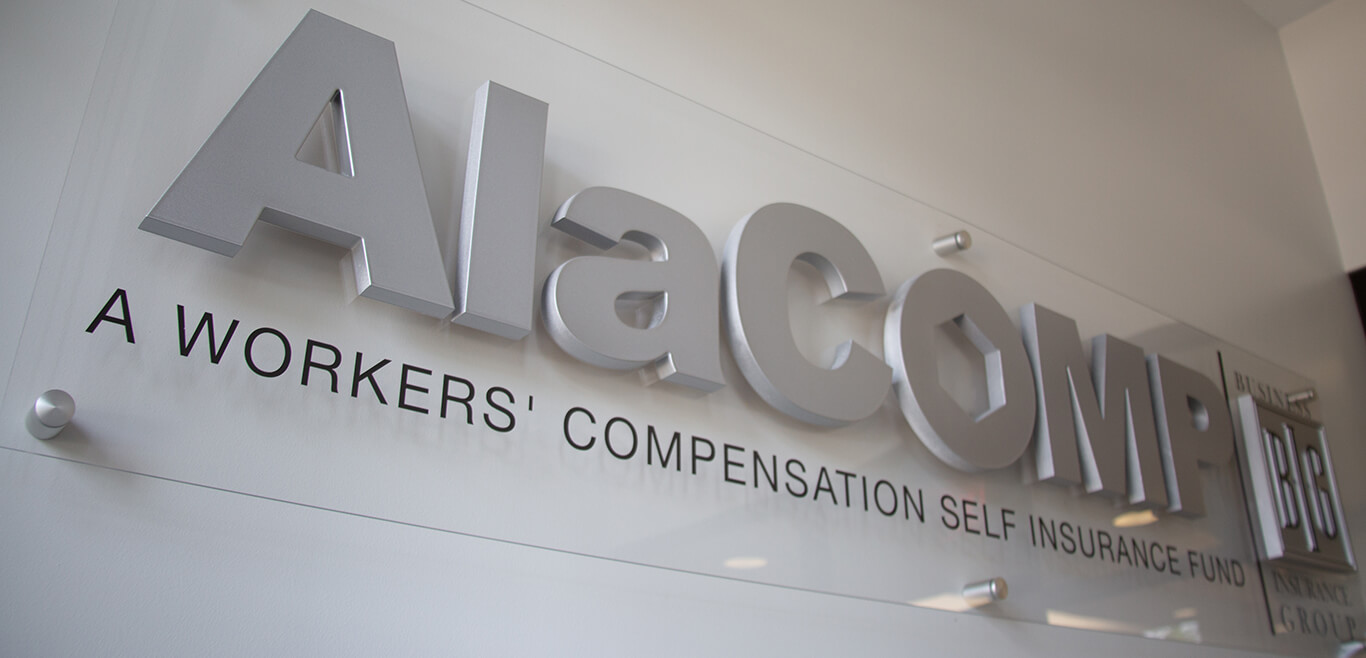
AlaCOMP provides news and OSHA Updates to all members. Each entry is packed with vital safety tips, updates to claims processes and information on the annual seminar devoted to safety and workers’ compensation subjects.
Safety Alert: Safety Responsibilities for Supervisors
November 17, 2021
Supervisors are responsible for many tasks in the workplace. However, a supervisor's job is not strictly assigning tasks- supervisors must ensure a safe and healthful workplace for employees. Their responsibilities extend to the following: Orientation and Training- Training and instructing employees to perform their work safely is a vital supervisor responsibility. Supervisors should educate employees on what PPE is needed and how equipment is used, stored, and maintained. Enforce Safety-…
MORESafety Buzz- October 2021
October 29, 2021
October 2021 Making Every Claim a Big Deal What are some of the various impacts an insurance claim has on a cmpany? Maybe it is a minor vehicle accident. No injuries so no big deal, right? Well, that is where, as a company, you could go horribly wrong. Every claim that occurs within an organization must be a huge deal! In fact, it needs to be the single most significant event that happened on that day. You might ask why should we…
MORESafety Alert: Do You Have the Proper Lighting?
October 20, 2021
Improper Lighting When we think of hazards in and around the workplace, often times we consider heavy machinery, power tools, chemicals, and electrical hazards, just to name a few. One item that is easily overlooked is proper lighting. Whether it is indoors or outdoors in areas such as parking lots, improper lighting can be a serious hazard. In this piece we will focus on the topic in two sections. The first section will touch on a couple of hazards associated with insufficient outdoor…
MORESafety Alert: Maintaining Safety Data Sheets (SDS)
October 14, 2021
OSHA requires safety professionals to maintain Safety Data Sheets (SDS) in the workplace for all substances that contain hazardous material. Safety professionals often get asked what is a SDS? Where do you get them? How must they be maintained? Do they have to be printed? We will try to answer some of those questions. What is a Safety Data Sheet? The SDS underwent its final change in 2015 from MSDS (Material Safety Data Sheet) to…
MORESafety Alert: 5 Steps to Ladder Safety
October 11, 2021
Ladders in the workplace are used commonly and often the safety aspect and training are often forgotten. 20% of fatal and lost workday injuries are from falls from ladders. Most of these accidents can be prevented if we follow the safety training and procedures. Below are 5 steps to ladder safety: Choose the Proper Ladder for the Job. Performing a quick job safety anaylsis (JSA) will help determine whether a step ladder or extension ladder is appropriate for the job. Inspect the…
MORESafety Alert: LOTO- Lockout Tagout
September 30, 2021
Is your Lockout Tagout (LOTO) program up to the standards for OSHA? The LOTO: Top 4 Reasons for OSHA citations video will provide the top reasons why OSHA gives citations and will help you to understand what is necessary to avoid these types of citations. Click the video below to watch: If you need additional information please visit our online safety library or if you have any questions or need assistance please contact our Loss Control Department.
MORESafety Alert: Top Items to Collect When an Injury Occurs
September 23, 2021
After every injury collecting the proper items/documentation necessary helps to ensure that the claim can be filed and handled quickly and properly. If there is missing information on the FROI or missing documentation this can effect how quickly a claim can be handled. Please find below the top 10 items to collect after a workplace injury occurs to help avoid any issues with handling a claim: Report the accident immediately - regardless of how minor the injury or accident may be, it should be…
MORESafety Alert: Keys to a Safe Construction Site
September 17, 2021
Construction Work is responsible for three work-related fatalities a day, per year on average. Overall, one out of five deaths were in construction. Some important considerations for having a safe construction site are as follows: A Safe Work Assessment should be in writing, outlining the scope of work and hazards present. The competent person should be identified as well as the entire chain of command. In addition, 24-hour emergency numbers, the location of the nearest medical treatment…
MORESafety Alert: Landscape Safety
September 13, 2021
As with any industry, safety is a critical element of landscaping and lawn care companies. With the ever-changing seasons and unpredictable weather, safety is a 12-month endeavor for landscape professionals. The best way to set yourself apart from the competition is to implement solid safety practices. First, this helps the company be more profitable, and secondly, it makes your company a place where employees want to work! Operating…
MORESafety Alert: Hierarchy of Control - Elimination, substitution/engineer, administration, PPE
August 26, 2021
The Hierarchy of Controls is a method of controlling hazards created by the National Institute for Occupational Safety & Health (NIOSH). NIOSH was founded in 1970 and is a United States federal agency responsible for conducting research and making recommendations for the prevention of work-related injuries and illnesses. The NIOSH Hierarchy of Controls is used as a means of determining how to implement feasible and effective control solutions to…
MORE