Top 10 Accident Causes of 2020
|
|
Each year we review a number of different metrics and data points from the previous year that are related to different claim types. This helps us to pinpoint areas of concern and where we are best suited to focus our efforts for safety messages and resources as it relates to accident prevention. Below, you will find the top ten causes of injuries for the fund year 2020. You will see that most of the usual suspects are again found in the top 10. Slips, trips, and falls is almost always one of our top producers of workers’ comp claims. There are also multiple categories related to material handling types of issues such as object handled, lifting, pushing and pulling, and object being lifted or handled. As we continue through 2021, use the below data to see if there are areas of your company safety programs that can be improved to prevent not only these, but other types of injuries as well.
- Slips/Trips/Falls – 283 claims
- Miscellaneous/other (likely not classified) – 257 claims
- Object Handled – 208 claims
- Object being lifted or handled – 205 claims
- Lifting – 103 claims
- Caught in/under/between – 81 claims
- Pushing/Pulling – 80 claims
- Machine(ry) – 72 claims
- Fellow Worker/Patient (not a crime) – 67 claims
- Hand tool (not powered) – 54 claims
|
|
Amputations can be some of the most severe and traumatizing injuries that occur in the workplace. Injuries of this magnitude can lead to life altering changes for the effected employee. Aside from the serious injury to an employee, which is the most important aspect, these types of injuries can lead to several other issues as well.
Amputations must be reported to OSHA within 24 hours. This can lead to a follow up visit from OSHA to further investigate the injury, which could in turn lead to citations depending on the outcome of the investigation. Lost productivity is almost sure to follow the accident as well. Depending on the task that was being performed and the type of equipment that caused the injury, production lines may need to be shut down for an extended period for accident investigation procedures to take place, for the equipment to be inspected to ensure it is functioning properly, and for cleaning. Depending on the circumstances, amputations can also lead to a loss of employee morale and other employee issues related to the shock of the event, as more severe cases tend to be rather gruesome in nature.
From a workers’ compensation insurance perspective, amputations can be costly, but this depends on the severity of the injury and body part injured. Each of these scenarios are ones that no employer wants to deal with, but the most unfortunate part is that aside from each of the additional situations, there is still an injured employee, and that is main item we want to prevent. Let us discuss a few ways that amputation injuries can be avoided:
|
|
Proper Training
Employees should never be given a task or assigned to a piece of equipment or machinery in which they have not been properly trained. This is one of the most basic steps to take when protecting your employee’s well-being. Make sure they understand all tasks delegated to them, and that they are competent to operate any dangerous equipment or machinery. The training should be thorough and documented by having the employee sign off on comprehension.
|
|
Machine Guarding
Any machinery or equipment with pinch-points or with the ability to cut or crush should remain always guarded. Employees, as part of their training, should be made aware of proper guard placement and should be comfortable to report any tools or machinery that have guarding issues such as missing or damaged guards. Employees should never operate equipment with guarding deficiencies until the issue has been corrected. Any problems with the tool or equipment that require work in an unsafe place beyond the guards lead us to our next point, lockout/tagout procedures.
|
|
Lockout/Tagout (LOTO)
Employees should be trained in proper lockout/tagout procedures, know their role as either an authorized or an affected employee. Authorized employees perform the procedures on a lock and tagged out piece of equipment by placing the LOTO device on the equipment and performing whatever service is needed. Affected employees are typically the machine operators or work in the area where LOTO work is being performed and cannot perform the LOTO procedures themselves. Any jams, blade changes, or maintenance performed in the equipment should only take place after proper LOTO procedures have occurred. LOTO procedures must be machine specific and only performed by authorized employees. Companies are also required to audit their LOTO program on an annual basis.
|
|
Working these three steps into your overall company safety program will, without a doubt, go a long way in lowering amputation risk and preventing undue harm to your employees. If you would like more information on employee training, machine guarding, lockout/tagout program, and accident prevention in general, see the AlaCOMP Online Safety Library where you will find a number of resources related to each of these topics or feel free to contact the Loss Control Department for further guidance.
|
|
Helpful Tips:
Ways to Improve your Workplace Safety in 2021
|
|
As everyone knows there are always ways to improve. Below are five helpful tips on ways to improve your workplace safety in 2021.
- Evaluate - What went wrong in 2020? What went right? What areas of safety had success and what areas of safety need improvement?
- Prioritize - Rededicate to make safety your #1 priority. From there, determine the areas that need the most focus in 2021.
- Lead - Safety starts at the top. Without strong leadership, there cannot be a strong safety program. Determine how to get your team to buy-in to your safety priorities this year.
- Communicate - Effective communication is the key to an effective safety program. Effective communication does not just include having employees attend a safety meeting; effective communication is constant, and it ensures employees have the knowledge and understanding of proper workplace safety.
- Listen and Evolve - Communication is a two-way street. Improve your workplace safety in 2021 by listening to your employees’ thoughts, concerns, and ideas. If they tell you something isn’t working, listen to them. They may even have a better idea than you about where your most severe hazards are.
|
|
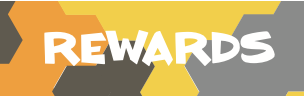
|
AlaCOMP-OSAA is continuing the Rewards and Recognition Programs for its members this year. Below are the details.
LOSS RATIO RECOGNITION PROGRAM:
Each quarter we will sort members by loss ratio into four categories – excellent, good, satisfactory and critical. We will notify each member in regard to the category they fall into and offer suggestions for improvement, if necessary.
LOSS RATIO DRAWING:
We will review all members' loss ratios on Sept. 30, 2021. Each member in the top 3 categories (excellent, good and satisfactory) will be entered for a drawing to win a specified amount off their 2021 renewal premium. The drawing will be held Oct. 5, 2021 with a total of 6 winners.
**This is a use it or lose it program. To receive the credit the member must renew with AlaCOMP in 2022.
LOSS CONTROL REWARDS PROGRAM:
There are two different rewards programs offered that all members can participate in for a chance to win a specified amount off their 2022 renewal premium. Details regarding each rewards program are below:
- Safety Library Rewards Program: If a member logs into the safety library and downloads material between Jan. 1 – Sept. 30, the member's name will be entered into the drawing. One entry per day.
- Loss Control Consultation Rewards Program: If a member has requested a loss control consultation from AlaCOMP from Jan. 1 – Sept. 30, the member's name will be entered into the drawing. A consultation can consist of a visit, safety library training, phone call, etc.
All drawings will be held on Oct. 5, 2021. There will be 1 winner per category.
**This is a use it or lose it program. To receive the credit the member must renew with AlaCOMP in 2021.**
|
|
AlaCOMP News
As we continue to navigate the new normal, we are all finally back in the office. For AlaCOMP, 2021 has been a wonderful year so far and we look forward to what is in store next. We have celebrated retirements, new employees joining our team, anniversaries and birthdays this year. As we continue to strive to provide the best customer service to all our members, if you have any questions or need help on any issues, please feel free to reach out to our office at 334-215-8234.
|
|
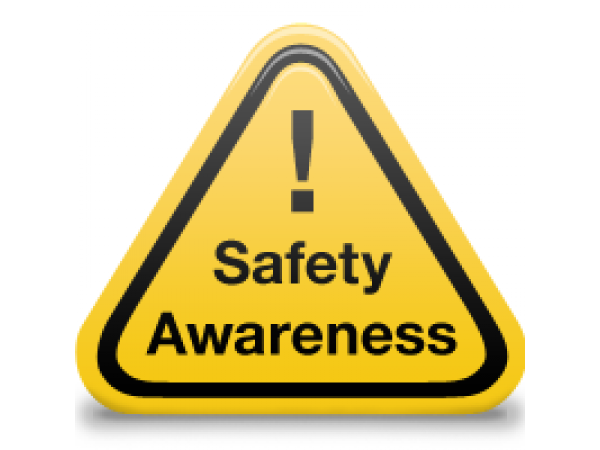
|
For the months of July, August and September we will be highlighting:
- Heat Stress
- Lifting, pushing, pulling
- Hierarchy of control: elimination, substitution/engineer, administration, PPE
- Restaurant safety
- Landscapers/outdoor companies
- Emergency Plans
- Construction
- Safety Manager Software
- LOTO Program
For the months of October, November and December we will be highlighting:
- Ladder Safety
- SDS
- Distracted Driving
- Pinch point
- Mainstreet retail
- Proper lighting
- Safety Library/Loss Control
- How to train supervisor/employees properly
If there are any additional topics you would like to see from us, please email Kelly.
|
|
Online Safety Library:
Creating modules within the Learning Management System
|
|
Did you know that you could create modules for your employees to complete within the AlaCOMP Online Safety Library? Our Safety Library has a fully integrated Learning Management System (LMS) that allows users to create password protected modules for designated employees to complete. You will assign a password to the employee and they will only have access to the modules you have created and assigned to them. Any item in the Safety Library that has the term “course” next to it also offers a quiz for the employee to complete and produces a certificate that they can print. You will be notified that the employee has completed the assigned course and their proficiency on the quiz.
Handouts and PowerPoint presentations can also be assigned to the modules for the employees to review. This can be an effective alternative or a supplement to your formal in-person safety meetings. There is a video tutorial on the safety library that will walk you through setting up and utilizing the modules. Feel free to contact the Loss Control Department for more information on the module set up or the Safety Library.
If you need access to the safety library or help logging in, please contact Scott in our Loss Control/Risk Management Department.
|
|
If you have any questions, please contact our Loss Control Department:
|
|
Top 5 Tips for Preventing Machine Guarding/Crushing/Amputation Related Injuries:
|
|
OSHA Standard 1910.147 covers the servicing and maintenance of machines and equipment in which the unexpected energization or startup of the machines or equipment, or release of stored energy, could harm employees. This standard establishes minimum performance requirements for the control of such hazardous energy (OSHA, 2021). Lockout/Tagout compliance is a critical piece of any effective safety program. Proper Lockout/Tagout Procedures prevent accidental startups of machines and other energy sources during maintenance or repair activities. Below are 5 tips to help ensure your Lockout/Tagout Program effectively keeps your employees safe on the job:
- Lockout/Tagout Evaluation - Every workplace is unique. The first step in an effective Lockout/Tagout Program is evaluating your facility to identify the specific needs your workplace will require and listing all machines and energy sources that might require lockout devices. Different machines and other energy sources require different locks so having the proper locks in place for your specific facility is an essential part of an effective LOTO Program.
- Isolating Energy Sources - After evaluating what devices require lockout/tagout procedures, it is important to choose the correct procedures for that device. For example, is the machine even capable of safely being locked out? If the answer is no, then a tagout device and program is required to ensure that employees working on energy sources are protected. A tagout program must allow employees the same amount of protection as a lockout program would.
- Training - Proper employee training is a critical part of an effective LOTO Program. First, we must understand the difference between an affected employee and an authorized employee. An affected employee is an employee whose job requires them to operate a machine or equipment in which servicing, or maintenance is being performed under lockout/tagout or works in an area where such servicing or maintenance is being performed. An authorized employee is a person who locks out or tags out equipment to perform servicing or maintenance on that machine or equipment. Affected employees should be trained on the hazards associated with LOTO at least annually, and they should also understand that they are not to perform servicing or maintenance on any machines or equipment. Authorized employees require annual training that covers the hazards associated with LOTO and the safety procedures to follow during service or maintenance. Authorized employees should also be evaluated at least annually to ensure that they can properly follow all LOTO procedures.
- Evaluate Internal Procedures - No matter how great your Lockout/Tagout Written Program is, a culture or procedure that does not support proper lockout/tagout can reduce your program’s effectiveness. Policies and procedures may “incentivize” skipping LOTO by requiring work to be done in a certain period. Employees who feel they are being rushed to complete a job will inevitably take short cuts, therefore it is important to make sure your culture fosters a safe LOTO Program.
- Adapt to Change - As with anything else, there is always a new and better way to do things. Encouraging communication with employees is one way to figure out what is working and what is not. Additionally, OSHA requirements may also be updated, and new technology may come out. However, when these changes inevitably occur, make sure that change is properly communicated with your employees and training exercises can take place.
|
|
As we continue to encounter mail delivery service delays we want to remind you that you can negate the mail service completely by paying via ACH. ACH payments can be done on our online portal as a one-time payment or a reoccurring payment. This would eliminate writing and mailing a check and then worrying about whether it will be delivered on time or not.
If ACH is something you are interested in and you have questions or need assistance with logging in, please contact Stephanie Belser at (334) 215-8234 or sbelser@alacompins.com.
If you do pay by check, please remember to include your payment stub for quick and easy processing. The lockbox will not process payments unless there is an accompanying payment stub. Payments received without a payment stub must be manually processed, increasing the risk that the payment will be misapplied. Please ail your check to the following address:
AlaCOMP
Dept B, P.O. Box 830520
Birmingham, AL 35283
|
|
|
|
|